How Has Mosaic Done in Terms of Raw Material Costs?
Mosaic purchases certain raw materials at fixed costs to be consumed over time, but the selling prices of its finished goods can fluctuate rapidly.
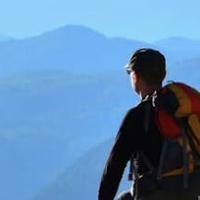
March 29 2016, Published 2:17 p.m. ET

Cost of goods
When evaluating commodities companies such as Mosaic (MOS), PotashCorp (POT), Agrium (AGU), and CF Industries (CF), we must also look at their production costs. Managing costs becomes key to profitability, especially in the case of commodities companies, since they compete primarily on costs for standard products such as DAP (diammonium phosphate) and MAP (monoammonium phosphate).
Mosaic’s business is vertically integrated, which means that the company owns phosphate and potash mines as well as production and processing facilities.
Mosaic’s cost of goods includes the cost of the raw materials that go into making crop nutrients. The company purchases certain raw materials at fixed costs to be consumed over time, but the selling prices of its finished goods can fluctuate more rapidly than its ability to consume these materials. A fall in raw material costs greatly benefits Mosaic and helps protect its margins.
Prices of DAP have moved in tandem with the raw material costs of ammonia and sulfur, as can be seen in the chart above. Ammonia prices have fallen over the years as a result of falling natural gas prices. Sulfur, which is a by-product of oil, has also trended downward.
Higher costs per ton
Mosaic’s Potash segment faces particular risk as a result of the brine flow it uses in solution mining, which we discussed earlier in this series. This increases the cost per ton of its potash production.
In 2015, Mosaic spent $160 million–$180 million in brine management costs. As a result, Mosaic is on the higher side of the cost curve compared to other Canpotex members. Canpotex members include Mosaic, PotashCorp (POT), and Agrium (AGU). The VanEck Vectors Agribusiness ETF (MOO) holds about 3.7% of Mosaic.
Next, we’ll explore Mosaic’s cost curves in more detail.