How does coke fit into the steelmaking process?
Iron ore, steel scrap, and met coal are the main raw materials for steelmaking. SunCoke converts met coal to coke by driving out its impurities.
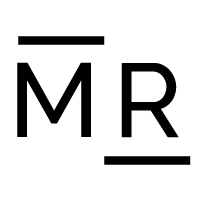
Jan. 2 2015, Updated 4:12 p.m. ET

Steel’s strong foundation
Steel holds special significance in the world. In the late nineteenth and early twentieth centuries, steel propelled development in the United States as technological developments and an abundance of raw materials led to dramatic growth in US steel production. Steel production in the United States grew from 30,000 tons in 1875 to a massive 60 million tons in 1920. The rise in steel production was supported by growth in the infrastructure and automobile sectors, building a strong foundation for the American economy (SPY). More recently, China’s path to growth has been supported by steel.
Key raw materials
Iron ore, steel scrap, and met coal are three main raw materials for steelmaking. Thus, growth in steel production positively impacts met coal producers (KOL) such as Walter Energy (WLT) and Alpha Natural Resources (ANR). Met coal is converted to coke (almost pure carbon) by driving out impurities. This is done by heating met coal in the absence of air in coke ovens. That’s what SunCoke Energy (SXC) does in its coke making segment.
Steelmaking
Coke and iron ore, along with other minerals, are heated in a furnace to make iron. Following are the two methods used to convert molten iron to steel:
- Basic oxygen furnace (or BOF). The BOF process uses 25%–35% old steel (scrap) to produce new steel. On average, this process uses 1,400 kilograms (or kg) of iron ore, 770 kg of coal, 150 kg of limestone, and 120 kg of recycled steel to produce a ton of crude steel. Around 40% of steel in the United States is made through this process. As this process uses mainly iron ore, the cost of production depends on iron ore prices.
- Electric arc furnace (or EAF). The EAF process almost entirely uses scrap steel to produce new steel. On average, EAF uses 880 kg of recycled steel, 150 kg of coal, and 43 kg of limestone to produce a ton of steel. It accounts for 60% of steel production in the United States. As this process uses mainly steel scrap, the cost of production is affected by steel scrap prices.
Now that we understand the steelmaking process, let’s see how SunCoke Energy (SXC) fits into the value chain.