Why Toyota’s Just-in-Time Method Is Critical to Its Success
Toyota began using the Just-in-Time method in 1938. However, the true potential of this strategy was realized when it integrated this strategy with TPS.
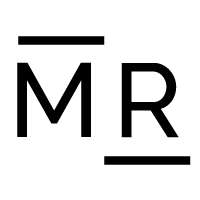
May 30 2016, Updated 11:08 a.m. ET

Toyota’s Just-in-Time method
The automotive industry is highly capital-intensive in nature. This is the driving reason behind efforts by automakers (XLY) to employ cost-effective business strategies to minimize their costs. The Toyota Production System (or TPS) is one of the most notable business strategies utilized by the automaker.
The Just-in-Time (or JIT) method is an integral part of this strategy. In this part of the series, we’ll explore how Toyota’s (TM) Just-in-Time method evolved and helps the company to minimize its costs.
Evolution of the Toyota Production System
After World War II, the majority of Japanese companies, including automakers, were facing challenges and struggling to survive. At the time, a sharp decline in auto demand and the high costs of production haunted automakers, including Toyota.
Toyota began using the Just-in-Time method in 1938. However, the true potential of this strategy was realized when it integrated this strategy with TPS. The company notes that this system was based on the concept of “the complete elimination of all waste.”
According to the company, “The TPS has evolved through many years of trial and error to improve efficiency based on the Just-in-Time concept developed by Kiichiro Toyoda, the founder of Toyota.” Additionally, a former Toyota vice president, Taiichi Ohno, is also associated with TPS. Ohno helped Toyota in creating the basic framework for the JIT method.
The company describes JIT as “making only what is needed, when it is needed, and in the amount needed.”
How does it work?
Using JIT, Toyota produces its vehicles based on the orders it receives through its dealers. In this production process, the company uses its supply chain in such a manner that only the parts that are needed to manufacture vehicles are received on time. Thus, the manufacturing and transportation of parts take place simultaneously. This allows Toyota to minimize its inventory of vehicle parts.
JIT also emphasizes the importance of work efficiency. According to Toyota’s website, the “use of JIT within the Toyota Production System means that individual cars can be built to order and that every component has to fit perfectly first time because there are no alternatives available.”
Notably, TPS has become very popular globally. It is also used by companies such as Hewlett-Packard (HPQ), Motorola (MSI), and General Electric (GE).
Now, let’s take a look at Toyota’s marketing strategy.