Steelmaking: An investor’s guide to the raw materials and process
Iron ore, steel scrap, and coal are three main raw materials for steelmaking. Steelmaking is a raw material–intensive business.
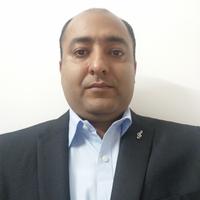
Oct. 29 2019, Updated 10:00 p.m. ET

Key raw materials in steelmaking
Iron ore, steel scrap, and coal are three main raw materials for steelmaking. Steelmaking is a raw material–intensive business, and it may not always be possible for steel companies to pass on the increasing raw material costs to buyers. It’s important for investors in steel companies like Arcelor Mittal ADR (MT), United States Steel Corporation (X), Nucor Corporation (NUE), Reliance Steel & Aluminum (RS), and ETFs like the SPDR S&P metals and mining index (XME) to monitor their movements
While there are multiple processes for steelmaking, we’ll analyze a very basic overview of the process.
The process simplified
There are two processes for producing steel:
- Basic oxygen furnace (or BOF): The BOF process uses 25%–35% old steel (scrap) to produce new steel. On average, this process uses 1,400 kilograms (or kg) of iron ore, 770 kg of coal, 150 kg of limestone, and 120 kg of recycled steel to produce a ton of crude steel. Around 40% of steel in the U.S. is made through this process. As this process uses mainly iron ore, the cost of production depends on iron ore prices.
- Electric arc furnace (or EAF): The EAF process almost entirely uses scrap steel to produce new steel. On average, EAF uses 880 kg of recycled steel, 150 kg of coal, and 43 kg of limestone to produce a ton of steel. It accounts for 60% of steel production in the U.S. As this process uses mainly steel scrap, the cost of production is affected by steel scrap prices.