Must-know: Why Nucor is different from its competitors?
According to Nucor “Empowerment isn’t a corporate buzzword—it’s a way of life.”
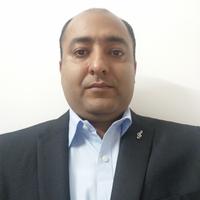
June 20 2015, Updated 3:02 p.m. ET
Why is Nucor different from its competitors?
Nucor (NUE) has one of the best labor productivity levels in the steel industry. Being cyclical in nature, the industry is characterized by frequent layoffs which results in labor problems. According to steel industry estimates, one out of two jobs are lost over a 30 year span. Nucor has had no layoff practice or history of labor tensions. The company treats employees as partners in its success. Most of the compensation of workers at Nucor Corp. is tied to performance goals and company profitability. According to independent estimates, around two thirds of average pay of a worker at Nucor is variable compared to ~20% at other steel companies like ArcelorMittal (MT), U.S. Steel Corporation (X), and Reliance Steel & Aluminum (RS). This serves the dual purpose of increasing productivity through a motivated workforce and keeping a check on labor costs in downturns.
The SPDR S&P Metals and Mining ETF (XME) is also an alternate way of investing into steel companies.
Giving power to managers
According to Nucor “Empowerment isn’t a corporate buzzword—it’s a way of life.” Each Nucor facility is run like an autonomous enterprise with significant powers in decision making. The general manager of each facility is responsible for the overall working of the plant. The company takes pride in having only 95 people in its headquarters. Empowering the managers helps in having a motivated leader and makes managers partners in the company’s growth. It also helps bring out fresh ideas. Nucor encourages the exchange of ideas. It has processes to ensure that ideas don’t get buried in bureaucracy.
Pioneer in mini mills
Nucor Corp. is a pioneer in mini mills. While most of the U.S. steel industry was making steel through blast furnace method, Nucor made new roads with the electric arc furnace (or EAF) and mini mills. The previous chart shows blast furnace and EAF in a simplified way. Today 60% of steel in the U.S. is made in EAF. The basic difference between the two methods is in the raw material used in steel making. While the blast furnace mainly uses iron ore and coal, EAF uses steel scrap and electricity. Apart from mini mills, Nucor also pioneered thin slab casting. It’s now focusing on direct reduced iron (or DRI) technology as we’ll see in the next section.